Evaluating the Electron Conductivity of an LIB Electrode Slurry
Applications
- Searching for materials
- Optimizing manufacturing conditions
- Screening slurries based on performance
Background
Battery electrode materials are used in the form of slurries that are diffused in a dispersion medium. Since the state of
dispersion in a slurry is unstable, it’s important to evaluate dispersion conditions as part of the quality control process.
In addition, since the slurry manufacturing process occurs at the beginning of battery manufacturing, screening needs
to be carried out at an earlier stage.
This Application Note introduces an application in which dispersion conditions are estimated by evaluating electron
conductivity in an LIB electrode slurry.
For more information about the principles underlying the Slurry Analytical System, please see this FAQ.
1. Differences in mixing time
Objective
To optimize mixing time
Slurry production conditions
- Solid content ratio
Active material: 95 % Conductive auxiliary agent: 2.5 % Binder: 2.5 %
- Mixing process
Mix for 0, 1, 3, or 5 min. with a solid content concentration of 70%
- Viscosity adjustment process
Dilute with NMP until the solid content concentration reaches 50%
Analysis results

Observations
With increasing mixing time, the Rratio decreased, and the DCR increased. These results suggest that shorter mixing time is associated with conductive material network development, which causes the slurry’s overall resistance to decrease. By contrast, uniformity increased with mixing time. This result suggests that longer mixing time is favorable for slurry dispersibility. When these results are combined, we can surmise that mixing time induces the following states in the conductive materials in the slurry, and that the mixing time of 3 min or longer yields a comparatively favorable slurry.
- Mixing time of 0 to 1 min
Conductive materials are in a state of agglomeration, resulting in short, and thick conductive paths. - Mixing time of 3 to 5 min
Conductive materials are in a state of dispersion, resulting in long, and thin conductive paths.
2. Differences in conductive auxiliary agent quantity
Objective
To verify the effect of adding conductive auxiliary agent as a way to reduce electrode resistance
To verify the relationship between slurry impedance and electrode resistanc
Slurry production conditions
- Solid content ratio
Active material: 18 g, Conductive auxiliary agent: 0.25 g, 0.5 g, 0.75 g, Binder: 0.5 g
- Mixing process
Mix for 9 min with a solid content concentration of 70%
- Viscosity adjustment process
Dilute with NMP until the solid content concentration reaches 50%
Analysis results
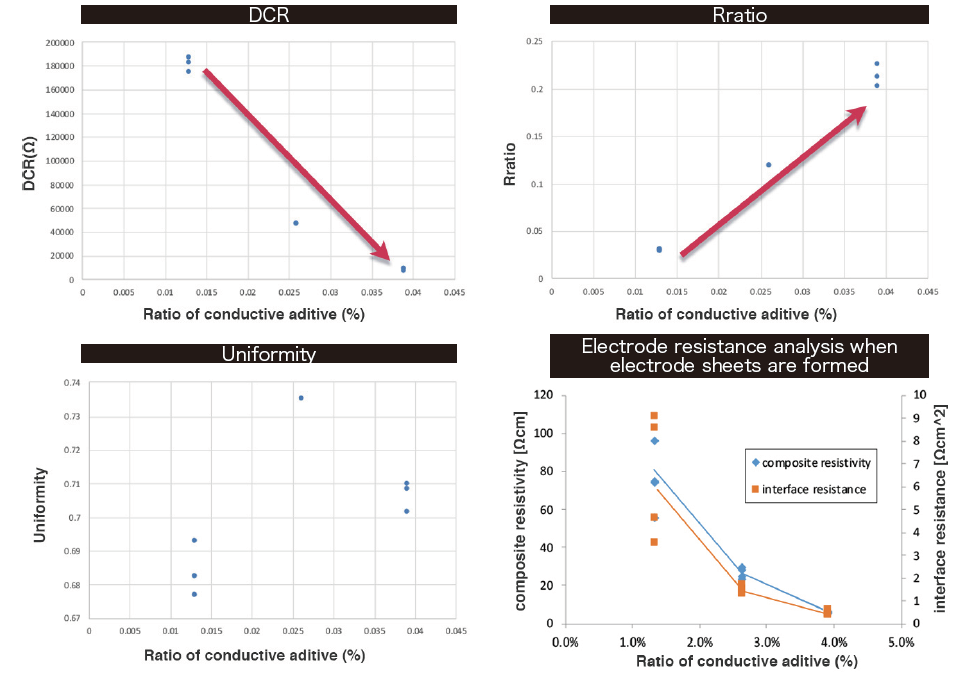
Observations
The Rratio rose, and the DCR fell, when the quantity of conductive auxiliary agent was increased. These changes, which suggest that adding conductive auxiliary agent causes conductive material networks to develop in the slurry, lowering its overall resistance to decrease, are in line with the theory underlying slurry analysis. By contrast, uniformity with the 0.75 g of auxiliary agent was lower than with the 0.5 g. We can surmise that conductive material networks formed more readily with the 0.75 g of auxiliary agent, but that dispersion was insufficient.
We formed electrode sheets with these slurries and analyzed them with the Electrode Resistance Measurement System RM2610. The results indicated that both the composite layer resistance and the interface resistance fell as the quantity of conductive auxiliary agent increased. These results suggest that the slurry’s electron conductivity has been inherited by the electrode sheets’ resistance characteristics, indicating a good application process.
3. Relationship between electron conductivity and dynamic viscoelasticity resulting from differences in dispersant quantity
( provided by Shin-Etsu Chemical Co., Ltd. )
Objective
To verify the effect of dispersant quantity on a slurry using both in terms of impedance and rheology
Slurry production conditions
- Solid content ratio
Active material: 96 %, Conductive auxiliary agent: 2 %, Binder: 2 %, Dispersant: 0.08% to 0.16% (4% to 8% of the conductive auxiliary agent quantity)
- Conductive auxiliary agent slurry preparation
Preparation of a conductive auxiliary agent slurry containing only electrode auxiliary agent, dispersant, and NMP
- Electrode slurry preparation
Preparation of an electrode slurry by adding active material and binder
Analysis results
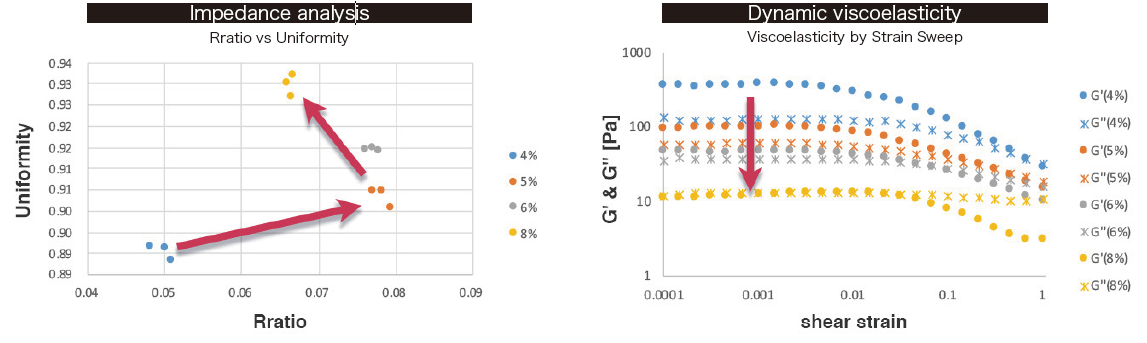
Observations
- Adding dispersant from 4% to 5% of the conductive auxiliary agent quantity
Rratio increased abruptly, and the difference between G’ and G’’ decreased.
These results suggest that adding dispersant eliminates agglomeration of the conductive auxiliary agent and that the conductive auxiliary agent networks formed are functioning as conductive paths.
- Adding dispersant from 5% to 8% of the conductive auxiliary agent quantity
We can surmise that adding even more dispersant will increase fluidity and improve the coating properties due to the slurry’s favorable G’’ value, while the reduction in Rratio means that the conductive auxiliary agent networks will become even thinner, leading to breakages.