Optimize LiB Production with Precise Electrode Sheet Resistance Measurement
Introduction
Lithium-ion batteries (LiBs) power the future of mobility, from electric vehicles (EVs) to portable devices, demanding high performance and reliability. A critical factor in achieving this is the precise measurement of electrode sheet resistance. By using advanced tools like the Hioki RM2610 Electrode Resistance Measurement System, engineers can accurately quantify resistance, unlocking insights into battery performance, material quality, and manufacturing consistency. This application note explores the key benefits of measuring electrode sheet resistance, offering practical solutions for researchers, production engineers, and quality control teams aiming to enhance LiB development and production. Understanding these advantages ensures better battery efficiency, durability, and safety for EV manufacturers and battery material innovators.
Benefits in Research, Development, and Scale-Up
Estimating LiB Cell Performance
Measuring electrode sheet resistance provides a vital indicator of lithium-ion battery cell performance. Resistance directly impacts current flow and voltage drop, influencing the battery’s overall efficiency. High resistance in the electrode sheet can restrict current, leading to reduced cell performance and potential energy loss. By tracking resistance variations with tools like the Hioki RM2610, researchers can predict cell behavior early in the development phase. For instance, identifying high-resistance sheets allows engineers to refine electrode designs, ensuring optimal energy output and extending battery life for EV applications.
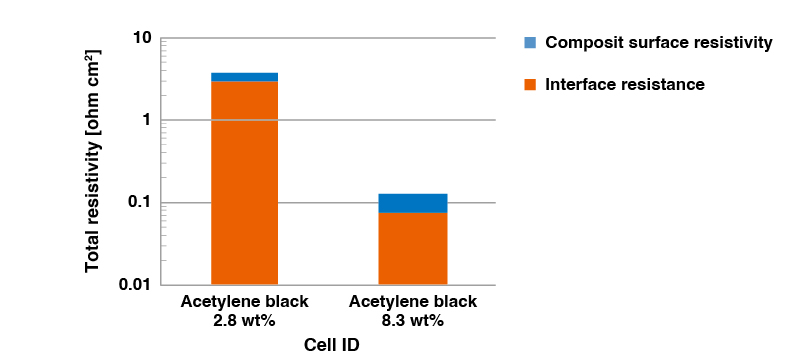
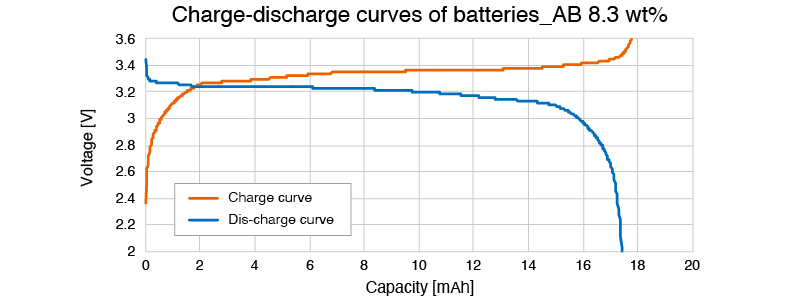
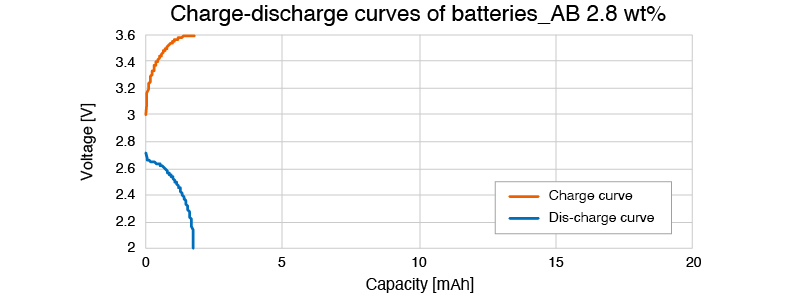
Understanding Material Properties
Electrode sheet resistance measurement is essential for evaluating the conductive properties of materials used in LiB electrode sheets. Different materials exhibit unique resistance characteristics, affecting the battery’s performance. By quantifying resistance, researchers gain insights into how material choices impact electrode behavior. This enables informed decisions during material selection, fostering innovation in battery design. For example, testing the effects of various conductive additives or binders with the RM2610 helps identify combinations that enhance conductivity, paving the way for next-generation LiBs with superior performance.
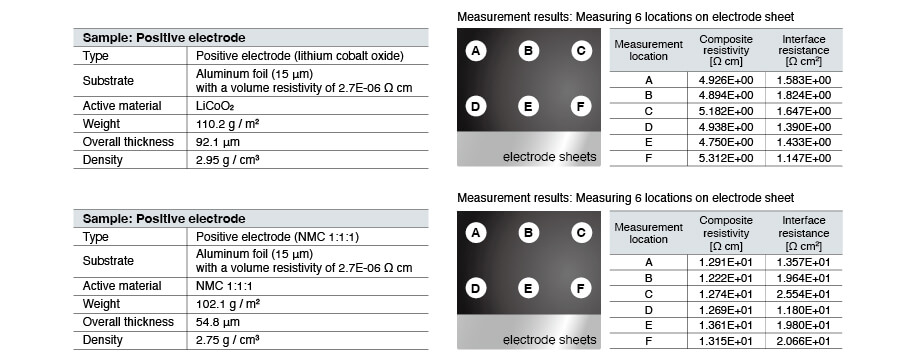
Optimizing Manufacturing Processes
Resistance measurement is a powerful tool for refining manufacturing processes during research and scale-up. Variations in mixing, drying, or pressing conditions can alter electrode sheet resistance, affecting final battery quality. By monitoring resistance with the RM2610, engineers can fine-tune these processes to achieve consistency. For instance, adjusting press pressure based on resistance data ensures uniformity across production batches. Additionally, resistance measurements help assess the impact of transitioning from small-scale R&D setups to large-scale production, minimizing quality risks during scale-up.
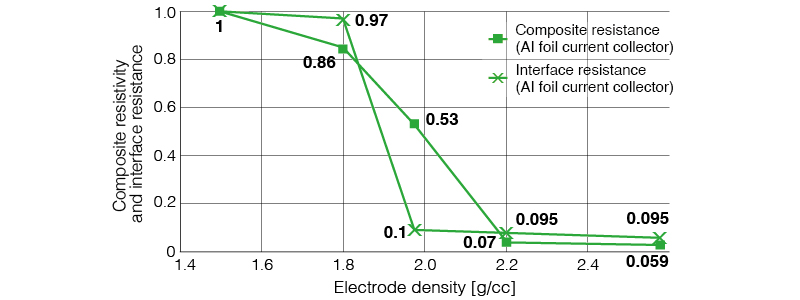
Analyze the effects of electrode density on interface resistance.
This graph illustrates the results of measuring an electrode while changing the press pressure to vary the electrode density. Although both the volume resistivity of the composite layer and interface resistance decrease as the press pressure and electrode density rise, the interface resistance drops precipitously after a certain point. The roughly constant value after that decline is useful in determining the optimal value.
Benefits in Production and Quality Control
Streamlining Sampling Inspections
In high-volume LiB production, resistance measurement enhances quality control through effective sampling inspections. Resistance variations signal changes in manufacturing stability or slurry uniformity, which traditional thickness measurements may miss. For example, the RM2610 can detect subtle process deviations, such as environmental shifts or equipment changes, that affect electrode quality. Conducting resistance-based sampling before and after batch changes helps identify potential defects early, preventing costly lot failures and ensuring consistent battery performance for EV and battery material applications.
Investigating and Analyzing Anomalies
When production issues arise, resistance measurement is a critical diagnostic tool. Abnormal resistance values often indicate material inconsistencies or process deviations, such as improper mixing or coating. By using the RM2610 to analyze resistance, quality control teams can discover the root cause of potential defects, such as raw materials or upstream processes. This rapid identification enables targeted corrective actions, reducing downtime and improving production reliability. For instance, a sudden spike in resistance could reveal a batch of defective conductive additives, allowing swift intervention to maintain quality standards.
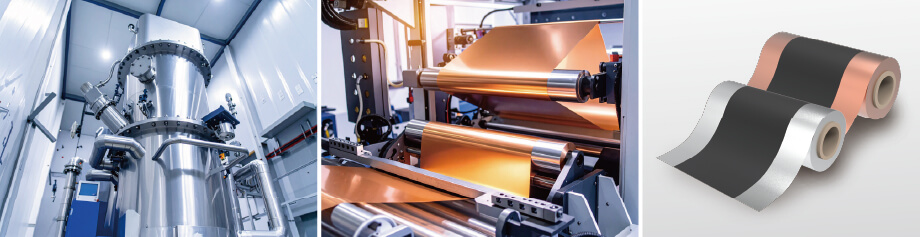
Conclusion
Measuring electrode sheet resistance with tools like the Hioki RM2610 delivers transformative benefits across lithium-ion battery development and production. From predicting cell performance and optimizing material selection to ensuring manufacturing consistency and enabling rapid anomaly detection, resistance measurement drives efficiency, reliability, and innovation. For R&D engineers, production teams, and quality control specialists, adopting this approach unlocks the potential for high-performance, durable LiBs that meet the demands of modern EVs and beyond. To learn more about enhancing your battery testing with precise resistance measurement, visit the Hioki website for detailed resources and solutions.
Discover how to optimize your LiB production—download our whitepaper at Hioki’s RM2610 product page.